One does not have to travel far to hear words like “unprecedented”, “historic”, and “extraordinary” used when describing construction material prices. Over the past year, COVID has shut down mills, assembly lines, and mines that produce many of the raw materials used in all types of construction. Simply, demand has far outstripped supply and that imbalance continues across large swaths of the construction materials sector today.
Lumber shortages have supplied some of the biggest price shocks within the construction sector. Any firm engaged in stick construction knows about the situation. The National Association of Home Builders (NAHB) reported that higher lumber costs have added nearly $24,000 to the construction costs of the average new single-family home.
But lumber costs aren’t the only category of construction materials going through significant inflationary pressures.
Rising Costs
There are many different measures that could be used to track construction material prices, but the Producer Price Index (PPI) provides a street level view of material costs. The index is based on survey respondents within construction firms and material producers, and it provides a blend of both contract and spot rates.
The latest PPI from March showed significant increases in core construction material prices whether comparing to the pandemic-impacted 2020 period, or stretching back to 2019.
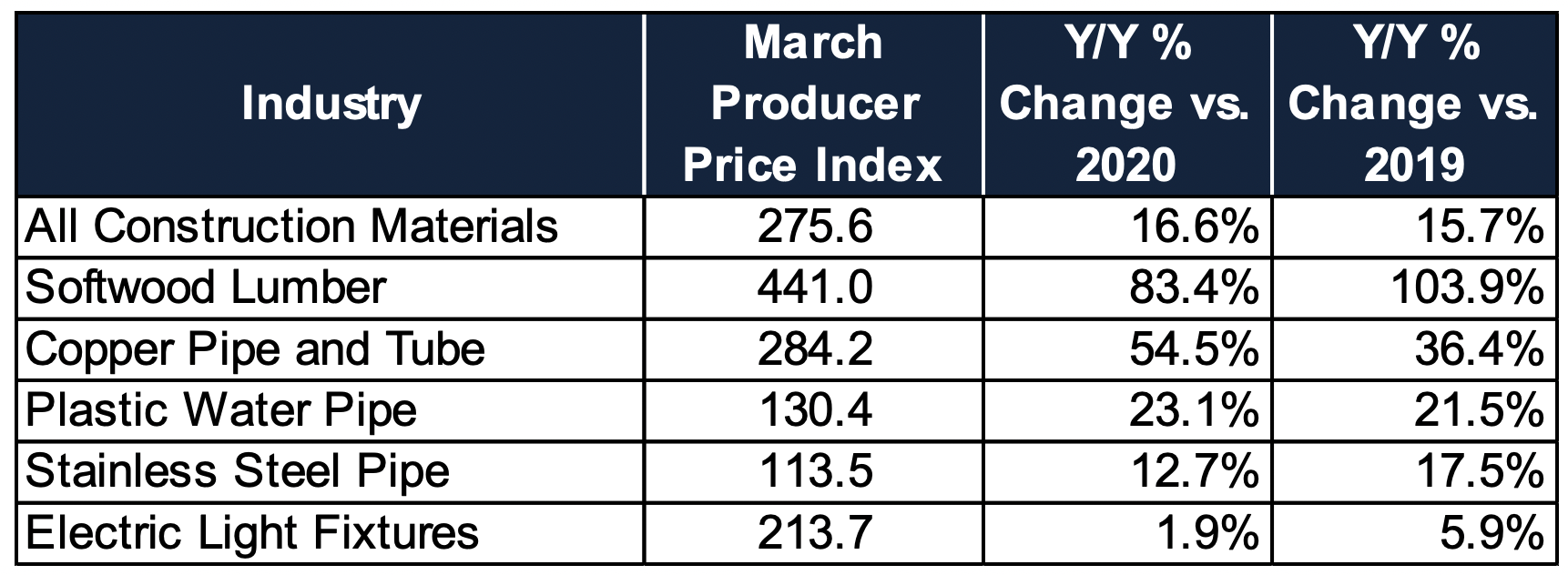
Copper pipe and tube prices were 36% higher than they were in 2019 and plastic water pipe was nearly 22% higher.
In addition, we currently see transportation costs to move these materials surging. Truckload spot rates in March as reported by DAT were up 41.9% over March of last year and were up 10.5% sequentially over February’s rates. Flatbed spot rates were up 7.9% month-over-month between February and March of this year. Including these costs in total material costs makes it a challenging time for costing.
Forecasts indicate that many of these supply/demand imbalances may continue well into the end of the year, and construction firms may not see material cost relief in the near term as a result.
Rising Demand in Home Building
The NAHB conducts a monthly housing survey and recently it showed a 3.8% month-over-month increase in the number of home builders that see strong growth in single family housing construction demand over the next 6 months. More importantly, it was 10.7% higher than it was a year ago during the pandemic. Home builders are confident that the home building market will remain strong through the next six months at a minimum, and perhaps through all of 2022 if interest rates remain historically low.
Some evidence of near-term strength in demand for new homes can be found in the latest housing permit data. US permits for new homes were 19.6% higher in February year-over-year and were 31.8% higher than they were in February of 2019. Some analysts believe that housing demand would be even stronger if new home prices were more affordable.
Federal Reserve Chairman Jerome Powell believes that these inflationary surges are temporary, and the Fed has resisted the urge to increase interest rates to tame the price pressure. The Fed believes that construction material shortages are largely a result of temporary supply outages and that these temporary conditions will alleviate supply pressure in the near term.
Construction firms of all types will face higher input prices. Labor shortages for many skilled workers are also pushing up labor costs. The latest national job openings report showed that the country had more than 7.4 million jobs open, a portion of these would be for highly skilled construction laborers. Hourly wages for construction workers around the country were 2.5% higher year-over-year in March.
Preparing for a Volatile Cost Environment
With construction firms taking on a volatile cost environment, it is important that firms do several things to prepare for the remainder of 2021 and well into 2022.
- Improve costing and supplier visibility
- Keeping in close contact with vendors and suppliers to ensure that a firm understands vulnerabilities in their supply chains.
- Getting supplier’s forecasts and estimates on when prices will adjust is also important in setting future expectations and being competitive in future bid opportunities.
- Unlock hidden cost control opportunities
- Unlock hidden opportunities to trim costs and increase efficiencies has never been more important.
- Use technology to help gather data and develop dashboards to have better visibility into costs. Building greater visibility into spending allows construction firms to better trim costs when appropriate and seeing it in an easy-to-digest format can help with rapid decision-making.
- Understand the details behind transportation and delivery costs (in an environment where shipping costs are up 40-50%) is a good way to trim costs and increase competitiveness.
- Understand a Changing Regulatory Environment and Maximize COVID benefits
- New waves of stimulus and spending bills could provide interesting opportunities and increase competition for scarce materials. The proposed infrastructure bill could pose both opportunities and lead to cost or regulatory threats. Understanding any new legislation and the impact it might have on taxation or tax benefits will be important.
- Changes in regulatory policy, especially green technologies, will be important to stay abreast of over the next two years or more.
As the US economy continues to open, the increase in nonresidential construction activity could further exacerbate price pressures on construction materials. After lying dormant for more than a year, many projects that were put on hold will restart and new projects will begin in some areas of the country. There may well be a race between the material supply chain getting back in cycle and the timing of significant increases in commercial construction activity (on top of a strong residential market).
In the meantime, volatility in the market and spiraling costs are immediate concerns. Gaining clear visibility into costs, trimming where possible, and forecasting with accuracy are simple ways of getting through this period.
MarksNelson can help you build a future for your business with the current challenges of the industry in mind. Reach out to us today.